|
Post by tech4 on Jun 26, 2010 10:48:11 GMT -5
I have seen a lot of TV advertisements for the Dremel Oscillating Tool and other makers with a similar device. Has anybody here tried one of those tools or found it worthwhile to take up space on the shelf? 
|
|
|
Post by franz on Jun 26, 2010 12:23:20 GMT -5
I'm still trying to find a 3rd use for my mouse sander. Don't have a sufficiency of planning time to buy anything new from Dremel.
|
|
|
Post by nutrivet on Jun 27, 2010 0:25:01 GMT -5
They are very useful at times. My carpenter friend uses them all the time
|
|
|
Post by tech4 on Jun 27, 2010 7:42:51 GMT -5
I read a lot of reviews and most all agree the Fein Multimaster is the best. It will cut nails and the Dremel will not. Still that is a lot of money to sit on the shelf for the few home jobs that I do. Now if I was a professional carpenter that's another story.
|
|
|
Post by markkw on Jun 27, 2010 22:57:52 GMT -5
I haven't use the Dremel but I did use some others. For generic application where appearance is not an issue, these can be time savers but they still don't get into tight corners - say you're going around a spindle attached to a step tread, no matter how careful you are, there's still going to be a ring around the perimeter of the spindle that can't be reached. I gave serious consideration to detail sanders for the gun work but have rejected all of them not only because of the missed area but also because the oscillation leaves either "fish hook" or "circles" from the abrasive in the work and these things will stand out like tens of thousands of little neon signs when the finish is applied. I've tried all sorts of things to get better detail finishing around carvings and while the cartridge rolls, flap wheels and coated sanding boards are quite handy, nothing works as well as good sharp chisels and scrapers when you need real detail and no scratches. The old art of using scrapers is pretty much lost to powered abrasives yet when some schmuck like me comes along using a scraper, it get attention. I was doing some body work on a '56 Ford p/u, dressing up the lower cab body line below the rear window. No way to power sand the cuved surface so I made a scraper to match the contour when the visitor, a life-long body man in his late 60's, was impressed enough to try it for himself. He was quite impressed at how easily the excess filler was trimmed off without making a cloud of dust whan hand sanding for hours. 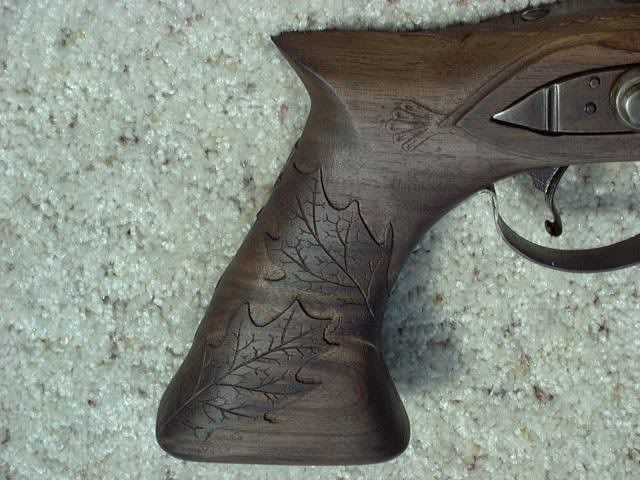 
|
|
|
Post by franz on Jun 27, 2010 23:47:03 GMT -5
Mark rest assured scraping is not a lost art. Back a few years when my dalin LN insisted she was painting the house, and insisted she could just scrape off the blisters I personally spent hours making her a set of scrapers from vehicle springs. She did a wonderful job with them, and I spent several more hours keeping them sharp because she knew I didn't know what I was saying when I told her scrapers only get pulled in 1 direction.
I think she has either hidden or thrown away those scrapers cause I haven't seen them in a long time.
Back in 02 I liquidated a shop that had made church furniture in the 1930s, and came across fiber drums of crushed garnate abrasive from Switzerland. A cabinet maker who had apprenticed there told me they used to make a plaster casting of details and glue the crushed garnate to the plaster for sanding. He bought every drum in the place for his shop. Evidently it is hard to come by today.
|
|
|
Post by markkw on Jun 28, 2010 8:52:09 GMT -5
Garnet is still available; I sell a few packs of garnet coated paper to a couple of wood workers but don't use it myself. Garnet is the softest of the natural abrasives and works best with medium to soft wood. The professional shops I supply mostly use AO (aluminum oxide) and SC (silicon carbide). On the metal working side, sanding/surfacing machines are running more Zi (zirconia) since the machinery has gotten better but depending on the application, AO is often more cost effective. Every application has to be evaluated and more often than not, the lifespan of coated abrasives can be easily multiplied simply by teaching employees how to keep the abrasives clean. On metal working machinery, I sell a stick lubricant that greatly increases both cutting efficiency and abrasive lifespan. In loose abrasives, AO & SC are still the most prevelent but thermo-silica is gaining more and more ground every day because it lasts a longer than glass beads but costs much less. It's also considered "green" as it is totally inert and non-toxic.
On the gun work I do, there isn't much abrasive use other than during the rough shaping stage, almost all the finish work is done by scraping and burnishing which is why the wood ends up with the natural sheen & glow with the silky feel, sanded finishes are rough looking and feeling, even people who don't know anything about wood can easily tell the difference.
PS, got the PM and will holler at you later about it.
|
|