Post by markkw on Aug 16, 2011 10:37:34 GMT -5
Todd asked about buffing compounds so here's the down & dirty abridged version:
First thing is that all compound colors are NOT standardized. I only deal with two trusted suppliers because their products are quality and their colors are standardized. Below is the short-list of the four primary low-grease compounds that will fill most all needs. I now stock four-pack of the low-grease compounds containing one bar each of Black Emory, Brown Tripoli, White Alumina & Ruby Red Rouge for $10.99 (Bar size 1.1” x 1” x 4.8” – I don’t go by mass because the mass will vary considerably according to the grease & moisture content of the individual bar making it an unreliable measure)
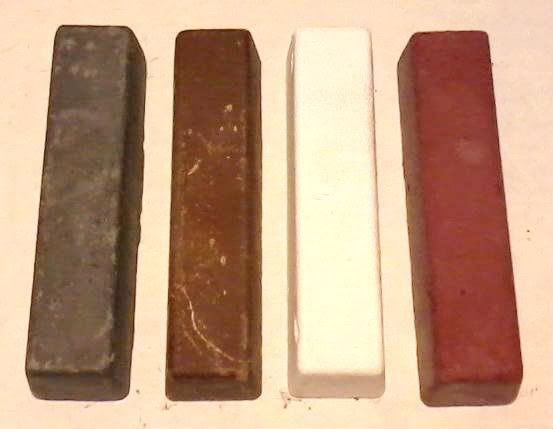
Black Emory – Heavy cut on all metals for removing scratches and smoothing surface. For removal of scratches and sanding marks, leaves surface shiny, semi-color buffed. Follow with Brown on most alloys to build color and finish polishing.
Brown Tripoli – Medium cutting on ferrous metals & stainless - fast cut on non-ferrous metals and plastics. Removes light scratches and sanding marks on all materials. Excellent for pewter, brass & copper. Follow with White on most materials (metals & non-metals) to build depth of shine and to enhance color.
White Alumina - Shine and color-building on most materials and is the only compound that should be used on light-colored porous materials to avoid staining or pore/grain-loading of the work.
Ruby Red Rouge - Final color building, low-grease compound is suited for all metals and most non-porous non-metal materials.
Each compound should have it's own buff, yes you can clean the buff to change compounds but all you do is wear down your buff which costs more time and money in the long run not only in buffs but wasted compound too.
I only listed the four primary compounds because these four will do most any common task - there are specialty compounds like Gold for high Chrome, & nickel alloys
Pink for Pewter and other Pb, Sn, Sb alloys (also works well on silver alloys)
Green falls between white and brown, works for intermediate cut on soft metals and low-cut on hard metals. This is a good all-around compound for general ferrous alloy work that's already been prepped and doesn't require going to a high degree of polish where one would need to follow it with White anyway. For aluminum alloys, Green is the typical go-to where it's not too aggressive but it will produce an acceptable final finish. For most people, Green ends up sitting around because one typically goes from Brown to White.
Blue - is an intermediate and/or final finish for synthetic materials depending upon the material and use method.
When buffing, direction matters! For cutting action the work is moved opposite the direction of the buff and for color & shine building the work is moved in the same direction as the buff. The amount of work to buff pressure that's applied will vary accordingly to obtain the desired results as too much pressure can cause burning, streaking and hogging and too little pressure can cause washboarding or compound plating where a layer of compound builds on the surface because there's insufficient pressure for it to work correctly.
The buffs themselves also matter. Most folks have little use for all the specialty buffs some retailers push as a way to boost their profits. I don't "push" anything except the concentric sewn 100% cotton muslin buffs because they are the most universal and you can pull a row or two of stitching to make it a loose face rather than pay a whole lot more money for one that just hasn't been fully sewn. The buffs I carry come in all sizes, most common are the 3"-8" diameter with a 1/2" arbor hole (will thread onto a 5/8" shaft). These buffs will last a long time if you don't abuse them, rake only when needed - I typically use a stiff wire brush rather than a solid tooth rake because the brush cleans just as good but without shredding the face of the buff. If you let me know what size buffs you want, I'll quote them because to list all the different ones I'd be here typing for a week.
I do carry some sizes of the laminated sisal/muslin buffs but I make it perfectly clear that these are very aggressive as in they'll groove work and take the hide and meat off your fingers about as efficiently as a grinding wheel. I don’t stock the treated buffs (yellow colored) because they’re another specialty item that doesn’t have much use other than in the small rotary hand tool sizes for detail work, the larger ones for buffers are good for compound profile work but care must be taken to keep from edge-cutting with them.
Standard 6”x1/2” muslin buff $4.15 – reinforced arbor hole $4.50
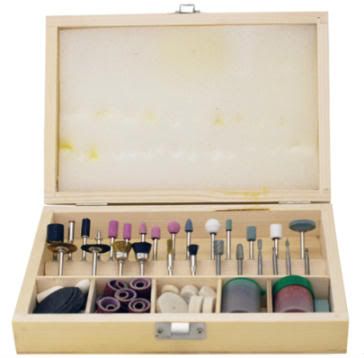
100 piece rotary set $11.99
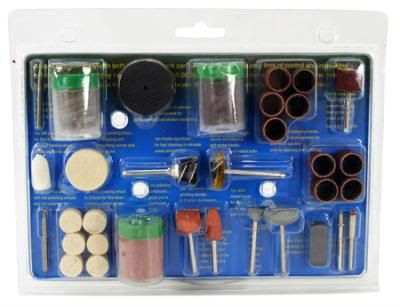
105pc rotary set $11.99
First thing is that all compound colors are NOT standardized. I only deal with two trusted suppliers because their products are quality and their colors are standardized. Below is the short-list of the four primary low-grease compounds that will fill most all needs. I now stock four-pack of the low-grease compounds containing one bar each of Black Emory, Brown Tripoli, White Alumina & Ruby Red Rouge for $10.99 (Bar size 1.1” x 1” x 4.8” – I don’t go by mass because the mass will vary considerably according to the grease & moisture content of the individual bar making it an unreliable measure)
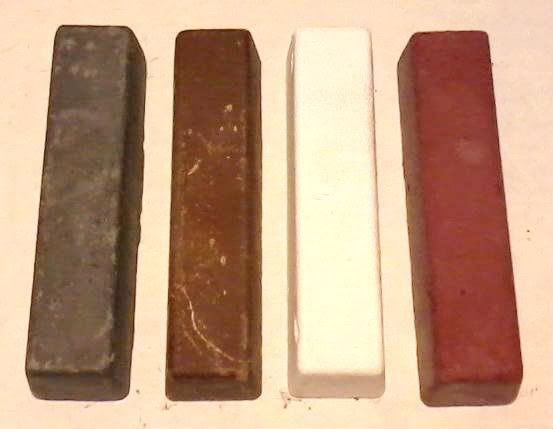
Black Emory – Heavy cut on all metals for removing scratches and smoothing surface. For removal of scratches and sanding marks, leaves surface shiny, semi-color buffed. Follow with Brown on most alloys to build color and finish polishing.
Brown Tripoli – Medium cutting on ferrous metals & stainless - fast cut on non-ferrous metals and plastics. Removes light scratches and sanding marks on all materials. Excellent for pewter, brass & copper. Follow with White on most materials (metals & non-metals) to build depth of shine and to enhance color.
White Alumina - Shine and color-building on most materials and is the only compound that should be used on light-colored porous materials to avoid staining or pore/grain-loading of the work.
Ruby Red Rouge - Final color building, low-grease compound is suited for all metals and most non-porous non-metal materials.
Each compound should have it's own buff, yes you can clean the buff to change compounds but all you do is wear down your buff which costs more time and money in the long run not only in buffs but wasted compound too.
I only listed the four primary compounds because these four will do most any common task - there are specialty compounds like Gold for high Chrome, & nickel alloys
Pink for Pewter and other Pb, Sn, Sb alloys (also works well on silver alloys)
Green falls between white and brown, works for intermediate cut on soft metals and low-cut on hard metals. This is a good all-around compound for general ferrous alloy work that's already been prepped and doesn't require going to a high degree of polish where one would need to follow it with White anyway. For aluminum alloys, Green is the typical go-to where it's not too aggressive but it will produce an acceptable final finish. For most people, Green ends up sitting around because one typically goes from Brown to White.
Blue - is an intermediate and/or final finish for synthetic materials depending upon the material and use method.
When buffing, direction matters! For cutting action the work is moved opposite the direction of the buff and for color & shine building the work is moved in the same direction as the buff. The amount of work to buff pressure that's applied will vary accordingly to obtain the desired results as too much pressure can cause burning, streaking and hogging and too little pressure can cause washboarding or compound plating where a layer of compound builds on the surface because there's insufficient pressure for it to work correctly.
The buffs themselves also matter. Most folks have little use for all the specialty buffs some retailers push as a way to boost their profits. I don't "push" anything except the concentric sewn 100% cotton muslin buffs because they are the most universal and you can pull a row or two of stitching to make it a loose face rather than pay a whole lot more money for one that just hasn't been fully sewn. The buffs I carry come in all sizes, most common are the 3"-8" diameter with a 1/2" arbor hole (will thread onto a 5/8" shaft). These buffs will last a long time if you don't abuse them, rake only when needed - I typically use a stiff wire brush rather than a solid tooth rake because the brush cleans just as good but without shredding the face of the buff. If you let me know what size buffs you want, I'll quote them because to list all the different ones I'd be here typing for a week.
I do carry some sizes of the laminated sisal/muslin buffs but I make it perfectly clear that these are very aggressive as in they'll groove work and take the hide and meat off your fingers about as efficiently as a grinding wheel. I don’t stock the treated buffs (yellow colored) because they’re another specialty item that doesn’t have much use other than in the small rotary hand tool sizes for detail work, the larger ones for buffers are good for compound profile work but care must be taken to keep from edge-cutting with them.
Standard 6”x1/2” muslin buff $4.15 – reinforced arbor hole $4.50
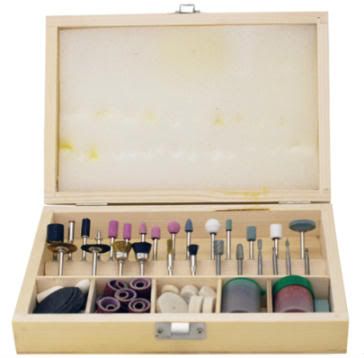
100 piece rotary set $11.99
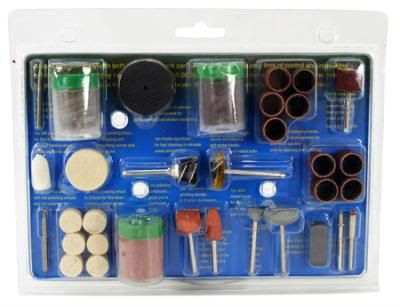
105pc rotary set $11.99