|
Post by bob on May 17, 2011 16:54:47 GMT -5
I just picked up a 1972 Lincoln Idealarc 250-250 welder and was wonder about 6010 rods. I've always used 6011 on an ancient AC Marquette welder on the farm, but with this new AC-DC welder I can go DC.
I was going to buy Lincoln 5P 6010 rod 1/8 and 5/32, but was wondering if anyone has tried ESAB's All-State Steelarc 80-LV red? Any noticeable difference as far as spatter, slag or just plain poor quality of the rod itself?
How is ESAB's consumables in general?
thanks...bob
|
|
|
Post by franz on May 18, 2011 12:27:31 GMT -5
6010 runs on DCRP, so does 6011. Ain't a dime worth of difference in my book, which dates to 1965. I grabbed it for a quick doublecheck before I posted and am still laughing that when it was published both rods were recommended for welding galvanized steel. The good old Pre OSHA days.
Personally I'd tell you unless you are in need of the fast freeze 10 & 11 provide, learn to weld with 6013. It will provide you with excellent welds IF you learn touse it and it's easy to run.
As far as difference between Lincoln, Hobart, Esab consumables they are damn near the same and the rest is salesmanship.
|
|
|
Post by bob on May 18, 2011 17:02:22 GMT -5
The 6011 I have I'm giving to my dad because he has an AC only machine. This is why I'm interested in the 6010.
I learned how to weld with 6011 (which was all we had on the farm) and then "graduated" to using a mig, when my uncle bought a Millermatic 200 a few years later. I like the 6011 (versus 6013) because of the penetration and the lack (or somewhat less) amount of slag that must be removed.
|
|
|
Post by markkw on May 19, 2011 7:16:33 GMT -5
6013LV is what you need but forget everything you knew about running off an AC power source. Jack the amperage up, bury the rod in the puddle and learn to weld in a makeshift sub-arc condition. Takes some getting used to but will make good welds.
|
|
|
Post by franz on May 20, 2011 1:57:14 GMT -5
Mark I get no end of enjoyment reading the postings of people who insist on going to 6010 or 11 for deep penetration when they are welding on ¼ material, and of course we all know 7018 MUST be used for strength on 2x2x¼ angle iron. Of course most have never picked up a rod book and insist 6013 is junk because engineers all spec 7018 for capping pipe.
If they had a damn clue they'd know 6013 and 7018 have damn near the same properties as welded. If they knew which end of the rod goes in the stinger they might have a clue that 6013 is the capping rod in half of Europe and most of Asia on pipe.
AND, as a fully qualified Broom & Shovel operator I will state for the record 6013 in no way brings the joy of shoveling up sand post cool. Hell, you can only run ¼" 6013 up to 375 amps by the book! That's only warmup for subarc.
|
|
|
Post by markkw on May 20, 2011 5:35:36 GMT -5
Franz, 6013 & 7018 have considerable differences both in operation and deposition. Other than special purpose electrodes, 6013 are V-down while 7018 are all-position. 6013 alloy has 0.6% or less manganese content while 7018 typically have 1.0-1.6% Mn. The coating is also vastly different in that 6013 are designed primarily for low-penetration low-dig operation allowing for use of a larger diameter electrode at lower current on lighter work but still allowing for moderate penetration with higher current operation. Biggest drawbacks to AC power sources is instability of the arc caused by the constant current reversal which only allows for 50% heat input to the work and causing 50% heat waste on the electrode. Secondly is the lower closed circuit voltage which reduces the available arc-directional control and when combined with the current reversal of AC it makes for a wildly wandering arc if the arc-gap is not maintained at absolute minimum. The primary coating composition is vastly different also 6013: 30-55% titanium dioxide; 2-12% cellulose; 10-15 potassium silicate; 5-10% clay 7018: 25-40% iron powder; 15-30% calcium carbonate; 15-30% flourspar; 5-10 ferrosilicone Common coating desciptions being: 6010 - cellulose sodium 6011 - cellulose potassium 6013 - titania potassium 7014/7024 - iron titania 7018/8018/9018/10018/12018 - low hydrogen iron Welding electrode(AWS E6013,E7018) Chemical composition(%) Mechanical Properties C Si Mn S P ¦Òb(MPa) ¦Òs(Mpa) ¦Ä5(% AWS E6013 ¡Ü0.10 ¡Ü0.35 0.3-0.6 ¡Ü0.035 ¡Ü0.04 ¡Ý490 ¡Ý400 ¡Ý22 AWS E7018 ¡Ü0.12 ¡Ü0.75 ¡Ü1.6 ¡Ü0.035 ¡Ü0.04 490-660 ¡Ý510 ¡Ý27 The major difference in the as-welded deposition is the reduction in area and Charpy V-notch ratings (tensile & yield are similar): 6010 - Reduction 60-64% / Charpy 32-34 ftlbs / T 75ksi / Y 62ksi 6011 - Reduction 22-60% / Charpy ¡Ü30 ftlbs / T 77ksi / Y 62ksi 6013 - Reduction 23-52% / Charpy ¡Ü25 ftlbs / T 72ksi / Y 60ksi The only spec's I have handy are the average for the particular E-7018 electrodes I use: Reduction in area - 77% Charpy V-notch - 90 ftlbs Tensile - 78ksi Yield - 68ksi For the intent of the OP's question, for buzz-box work the Esab 6013LV is the best choice if run as I described. Whereas a standard 1/8" diameter 6013 will run at 60-65 amp setting, penetration is absolute minimum and it's not uncommon to have a 3-5% inclusion factor. Bumping the amperage up to the 85-95 amp range will somewhat help reduce the inclusion factor but penetration is still barely moderate. Jumping again to the 120-130 amp range will increase penetration to the low-moderate range but at the same time increasing the likelihood of porosity/inclusions and spatter while further reducing the arc control. The 6013LV is a game changer only when operated correctly as stated. If you run them too low on amperage or don't have the coating in contact with the work, all bets are off. They must be run hot and tight to both work and puddle with no allowance for tricks like gap-bridging, playing the puddle with the arc or lead-in pre-heating as the slag will split/float the puddle and the weld will be worthless in terms of structural soundness. If run as I stated, they will produce acceptable quality welds with a good appearance but if the operator buggers, as with any 6013, underslagging and inclusions will be excessive. I'm no fan of Esab but their coating composition that produces the 6013LV does make it the optimum choice for buzz-boxes and they are far more user-friendly than standard 6013 & 7014 as long as the operator keeps the arc buried as I stated. Pipe welding is an interesting subject because more often than not, the spec'ed 7018 cap is for a combined appearance and to help make up for a poor/unknown-quality root pass. E6010 is the choice for X-ray quality pipe work and is plenty strong enough to survive destructive testing as the work will fail long before the weld provided the weld was done properly. When I was certified for OEM repair work by a particular European mfg, I had to submit six test samples on pipe assembled and completed at a 45¡ã angle, three samples utilizing consumable ring, three open-root. I did the test samples no differently than application work, no interpass grinding just brush clean only and hot-passing from root to cover-pass using only Lincoln E6010 5P+ for all passes. I can't even begin to tell you how many arguments ensued over 6011 vs 7018 and 7018 vs 10018 in coal mine & rock quarry work and all instigated by those who have no concept of welding process beyond getting two pieces of steel to stick together - unfortunately there plenty of those who should know better and don't too. Prime example is Caterpillar and other OEM's who seem to prefer making the claim "It can't be fixed" rather than accepting the facts. Sometimes that comes purely from the desire to simply sell new items but more often than not it comes from the lack of fabrication and/or materials knowledge. Example 1 is a 350 ton haul truck with the frame snapped clean in half vertically because of poor frame design. OEM and the know-nothing mine manager insisted the repair be done using E10018 and fish-plating with A546 despite the fact that neither the spec'ed electrodes nor the plate material was physically suited to the application. When I opposed those choices based on my own field experience, the mine owner hired an OEM approved shop to make the repair. Less than three hours of operation following their completion of the the spec'ed repair, the truck was again being rigged to limp it back to the staging area because the second failure of the frame was worse than the first. I was called back to make the repair my way, it took five times longer because of having to un-do the spec'ed work and contend with the addition damage it caused. My repair was done with standard A36 materials and E7018 electrodes - thousands of operational hours later that frame is still holding. 245 Cat excavator broken boom ear at stick pivot pin casting - "can't be fixed" (according to Cat & several other alleged "professional" repair shops). 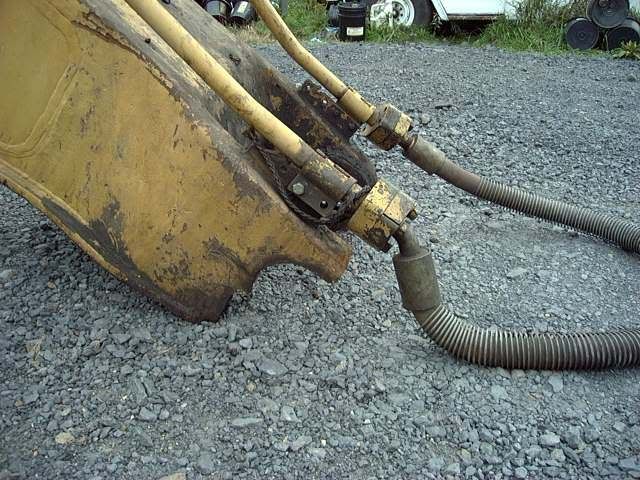 Same machine repair by me with a new fabricated ear installed on the OEM casting - many years and thousands of hours mining coal later, it's still going strong. 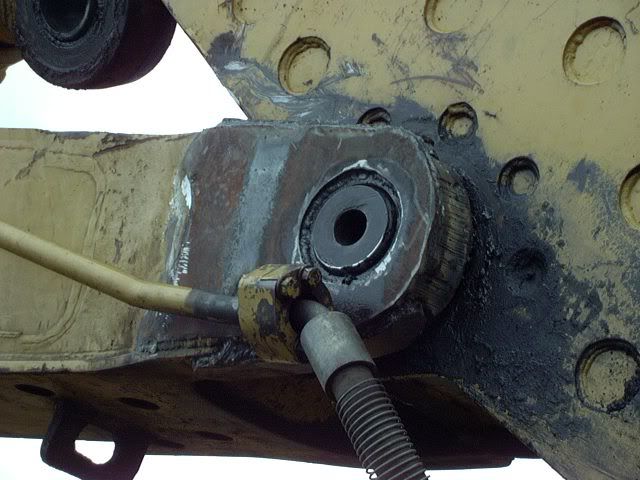
|
|
|
Post by franz on May 21, 2011 1:50:39 GMT -5
Mark you don't know the dirty little secret about CrapperPillar.
There is a little arrangement going back to World War II on their welding. The machines are welded by UAW members and the cylinders are welded in a separate building by members of a small union that works only in the cylinder plant. About 10 years back a whole new group of brilliant matriculated boys came to work at CrapperPillar in suits and hung their paper on the wall. They had computer models and charts that proved older workers should go out to pasture because young workers could be trained to be far more productive per dollar paid. Then they brought in a whole crop of manufacturing engineers with degrees and no damn protractor. They agreed with the management folks.
The first great experiment was in the cylinder plant. Crap bought out all the old farts who knew how to put cylinders together with the subarc process and not have them fail. The subarc was replaced by MIG, and oddly the manufacturing engineers didn't know MIG from piss. The new low cost production workers didn't know MIG either, so they brought in welding engineers who were sure the problems could be easily corrected with plasma welding.
Since none of the new welding process was working in the cylinder shop naturally management decided to get new MIG machines working in the fab plant with UAW members running them. CarapperPillar is loosing its ass and market the last few years because they have engineers who don't know which end of the machine the weld comes out of. The barely used plasma welders didn't solve the problems in cylinder manufacture so a large percentage of that work was moved out of the US. US made cylinders come apart still, and Crap is playing some very clever shit on owners when it comes to warranty. According to my bud who works in Ancorage the dealer there has 2 trailer loads of cylinders waiting to go back to Peoria for repair. By the time the tube has been repaired once following Crap's procedure there ain't a hope in hell of repairing the second failure. The dirty secret if you have to repair one is to go to 309ss on the first repair and burn it in.
Now it was real nice of you to write a whole book on 6013 -v- 7018, but it wasn't necessary. The only numbers that count in the real world are tensile 72,000 and yield 62,000 for 6013 and 78,000 and 66,000 respectively for 7018. 99% of the stuff people are planning to weld won't be more than ½, and since they either haven't got a clue what alloy they are welding on or won't make a damn phone call to find out, I just don't bother explaining much to them. Generally they'll wind up using a 120 volt MIG anyhow and I ain't got time to waste.
People don't want to learn the craft any more, they want instant weld in a box. I learned to run overhead 6013 on a AC box, and it made every other weld I ever made a lot easier to make. We had a 16 year old girl testing people coming in the door claiming to be weldors back in the 80s, and when she pointed to the AC machine and 1/8 6013 and told them to butter a 3" square with stringers 4 out of 5 left. She really enjoyed showing the mouthy ones how well it could be done.
BTW, you're right about CrapperPillar's design and material choice in the last 10 years too. Seems like they brought in experts from IH construction equipment to learn from.
|
|
|
Post by markkw on May 21, 2011 21:04:23 GMT -5
Franz,
Main points I intended to make on the 6013 vs 7018 is the depth of penetration, likelihood of porosity and the tremendous difference in the Charpy V-notch pressure ... which of course did not post as intended since the forum software obviously does not understand standard text encoding!
Esab has a winner with the 6013LV though, gotta give 'em credit for that one. You're correct in that for most home garage work, the vast majority wouldn't know the difference but anyone who is interested in learning will benefit from the information.
My issue with the Cat is that they insist "repair can't be done" purely for the purpose of making a sale on a new part. Any company worth its salt to their clients would not be so bold as to effectively say, "Screw you!". Unfortunately, there are many people who are now willing to blindly accept such nonsense and continue shelling out bucketfuls of their dollars based on nothing more than BS. There are those who argue the point that it's a liability issue when in reality, there's no more liability in making a repair than their is in building a new part - with years in the business building new and making repairs, I can assure you the liability is the same so that is a flat-out LIE.
I don't know about the cylinders, never paid any attention to them other than to make sure the bill got paid. Most common injuries (other than packing & worn eyes) were sheared off fittings, bent/broken rods and dented/crushed tubes. I worked with a local machine shop that had the capability of doing the big work, if a replacement cylinder wasn't available, between them and me, we could fab a new one in short order - if only the tube was bad, that's all that was replaced. I don't understand what the big deal is with putting a cap on a cylinder tube or an end on a rod, I've done them with both SMAW & GMAW. As my old Dutchie friend always said, "Ain't nuttin yaw fur dat ting."
|
|
|
Post by bob on May 22, 2011 11:33:26 GMT -5
Mark & Franz, the machine isn't the small buzz box (if it matters), but rather larger 350 pound tombstone Lincoln, that can handler 250 amp all day long, which is another reason I overlook the 6013 rod. I thought, take a 1/8 or 5/32 6010 rod and crank the amps up......
What I always did in the past would be to run 6011 for root passes and 6013 for the "cosmetic" appeal if needed. But because 95% of what I weld was for the farm or my own use, I never really cared for the pretty final bead that isn't really worth it. Plus, for me, it is a heck of a lot easier to weld in odd vertical or overhead with 6011 over trying to use 6013. I also find that welding in places where I cannot always clean the greatest, the 6011 will "blow" the crap out and not leave a poor weld, when compared to 6013.
As for 7018, my concern is storage. From what I read in the Lincoln book, it seems the fridge and bulb won't really work for long term storage. Second, if I can easily store 6010/6011/6013, why do I care about a 70xx rod? The extra tensile strength isn't going to help make the tractor loader stronger, because it is only as strong as the weakest weld, which is 45 years old, with who knows what for a rod/filler material.
Maybe my thinking is outdated, but it has worked for me....not saying I cannot change or improve......as soon as I get my new welder hardwired in.
thanks for the input, bob
|
|
|
Post by markkw on May 22, 2011 21:57:29 GMT -5
Bob,
The additional info helps. That machine will likely have a higher closed-circuit voltage so 6011 shoud run well. Keep the amperage reasonable because they'll get plenty of dig with the higher run voltage and if you use the cut & fill run method.
6011 are better at cleaning & floating junk out with the slag than 6010 or 6013. That machine should also do well with 7018 too, AC is a little different running, just keep a little more angle toward the puddle than you would with DC. 1/8" is going to be the most versatile diameter because you can turn them down for light work and run them at normal amperage for heavier work. 3/16" and larger in 6011 can get funky to run on AC depending on the composition of the flux coating.
Rod storage isn't all that big a deal, they need to be kept dry. Doesn't matter what the coating is, storage is all the same. I don't care for the lamp deal because they're too easily broken creating an electrocution hazard. Use a dedicated heating element, there are oodles of them to choose from, whatever fits your enclosure best. You don't need a whole lot of wattage, 15-25 watts is more than sufficient because all you want to do is keep the internal temperature about 10-15° above the ambient atmospheric temp. I don't like a refrigerator either unless it's an old one with all metal components, new ones are plastic lined and major fire hazard - of course, you can rip all the guts out. A steel filing cabinet works well, anchor the heater in the bottom drawer but make sure you have at least one pyrometer and one manual reset high-limit cut-out. Mark
|
|
|
Post by franz on May 23, 2011 0:10:11 GMT -5
Idealarcs ain't toumbstones! Idealarc is a moving core transformer and a toumbstone is a tapped transformer with a switch on the front that selects which tap you're using. The only similarity is Lincoln made both.
Idealarc comes in 2 generations, first with a rounded top to dump everything you set there on the floor, and second generation with a flat top. The flat top machines have a dummy protection circuit that lowers the OCV when the machine ain't welding because too many pussies cried they got a shock sticking a rod in the stinger. 1st generation is a magnificent machine, 2nd generation is repair bills.
As far as keeping 7018 in an oven, unless you're welding to code it ain't happening in most of the world. 7018 will suck and hold a lot of water, possibly more than other rods, but you aren't stopping that with a homemade oven.
Homemade ovens for noncode rod work don't need to be more than 20° hotter than the surrounding ambient to keep the rod from becoming the condensing surface. That's easy to achieve.
The job at hand defines the best rod to use, and I am totally against the concept of digging as a substitute for proper preparation. I've seen too many failed welds where the "welder" actually welding machine operator was sure he could dial it up and dig deep enough. If you don't have time to do it right to begin with where are you going to find time to redo it?
|
|
|
Post by bob on May 23, 2011 17:27:46 GMT -5
My machine is the older, round top; with the "eye-loop" in the middle for lifting this thing up. I paid $350 for it along with 100 feet of 1/0 cable. A Bernard stinger found its way to the welder, though I will admit though, I haven't used the new stinger yet. Re-roofing the barn has been my priority. The Lincoln has the PF capacitors which allows me the 50 amp input, compared to the 45 amp input for the smaller buzz-box machines, I figured this buy was a no-brainer. Cheaper price and twice the machine.
I never thought about using a filing cabinet or a heating element, but your right, its definitely a better idea over the bulb. Another idea was to use a surplus ammo/rocket box from Sportsman Guide or evil-bay, and had a heater to that. But, I got a earlier today that my Dad picked up a small fridge along the side of the road. I might just rip the plastic out, add sheet-metal walls and insulated (I have more insulation than I know what to do with) and get an element.
|
|
|
Post by franz on May 24, 2011 1:43:01 GMT -5
The PF caps are of little value unless you're buying power on a demand meter.
That old girl is one hell of a machine and should serve you well for along time unless you decide to mount it on a truck and go offroading. Take the cover off occasionally and use low pressure compressed air to blow the dust out. They tend to haul a lot in with the cooling fan. It's about as close as you can come to a sweet DC arc without going to a rotary machine.
|
|
|
Post by markkw on May 24, 2011 10:53:54 GMT -5
Bob,
Second what Franz said, the PF caps may help a little with smoothing the output if you're on a limited supply where you'll see a notable voltage drop upon closing the weld circuit - they should help reduce the tendency of spotting on starting the arc and whipping on breaking the arc. One thing I'll warn you about, if one of them PF caps lets loose, be absolutely sure you disconnect the power supply and maintain a short on all the conductors to ground before you even consider touching the machine case. I've seen them blow plates out to make contact with the case or lie in wait for some dumb schmuck to stick his fingers in there. Those caps store plenty enough juice to kill you many times over. Had one blow on a newer Lincoln, it took out the bleeder circuit when it came apart, what was left in the rest of the bank was enough to vaporize about 2" worth of what was a brand new Klein #2 phillips.
|
|
|
Post by Bathroomsrep on Mar 16, 2019 16:17:08 GMT -5
Good Night! Bathroom remodel gray and white Boerum Hill - <a href=https://bathroom-remodel.club>Bathroom remodel</a>
|
|